|
Written by Kristian Lauszus 
The PS4 controller is now also supported via Bluetooth. It uses the same API as the other libraries I have written, so if you have used them before, then you should be quite familiar with it.
The example code is available at Github: https://github.com/felis/USB_Host_Shield_2.0/blob/master/examples/Bluetooth/PS4BT/PS4BT.ino.
For more information take a look at my blog post: http://blog.tkjelectronics.dk/2014/01/ps4-controller-now-supported-by-the-usb-host-library/. This explains how to pair with the controller and have some background information as well.
You should also check out the readme which will always have the newest information available.
That is all for now. Hopefully this will be useful to anybody out there that wants to use the PS4 controller with the library.
Update 18. January 2014
A USB version of the library is now also available.
Written by Kristian Lauszus  PS3 keyboard
I am glad to announce that Bluetooth HID devices are now supported by the USB Host library. The library already supports PS3 and Wiimote controllers, but now you are also able to use Bluetooth mice and keyboards with the library.
An example is available at the following link: https://github.com/felis/USB_Host_Shield_2.0/blob/master/examples/Bluetooth/BTHID/BTHID.ino.
I have personally tested it with a PS3 keyboard (see image), an Apple Wireless Keyboard and an old Bluetooh mouse from Microsoft and all of them works fine.
For more specific instructions on how to use the library I recommend taking a look at the blog post at my own blog: http://blog.tkjelectronics.dk/2013/12/bluetooth-hid-devices-now-supported-by-the-usb-host-library/.
Feel free to post a comment below if you got questions or got problem with a specific device and I will answer as fast as possible.
Written by Kristian Lauszus 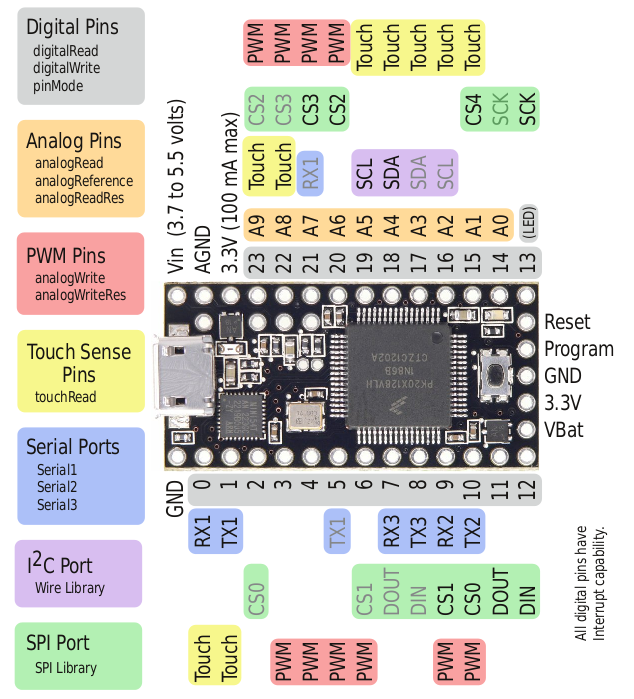 Layout of the Teensy 3.0
I am pleased to announce that the first ARM processor is now supported by the USB Host library. It is the Teensy 3.0 which features an 32 bit Cortex-M4 ARM processor running at up to 96MHz. This is a huge increase in speed if you are used to the Arduino Uno running at 16MHz.
The Teensy 3.0 is created by the Paul Stoffregen which is also a dedicated contributor to the Arduino IDE. If you are looking for a ARM based board for your next project, I recommend taking a look at the Teensy 3.0. A more detailed overview can be found at the official page.
To use the Teensy 3.0 with the library I recommend using the Mini variant of the USB Host Shield as it is much more compact and a bit cheaper too. Since the Teensy 3.0 is running at 3.3V no logic conversion is needed.
Note it is very important than you do not connect a 5V microcontroller to the Mini variant of the USB Host Shield, as this might damage the board. If you are planning to use a 5V microcontroller like the Arduino Uno I recommend getting the full sized version of the shield.
In order to use the Teensy 3.0 you will need to connect the Teensy 3.0 to the USB Host shield like so:
USB Host Shield |
Teensy 3.0 |
RESET |
3.3V |
GND |
GND |
INT |
9 |
SS |
10 |
MOSI |
11 |
MISO |
12 |
SCK |
13 |
3.3V |
3.3V |
GND |
GND |
The images to the right shows both the pinout for the Teensy 3.0 as well as the Mini USB Host Shield.
 Layout of the USB Host Shield Mini variant
Furthermore I recommend cutting the VBUS jumper and then soldering a wire from the provided pad on the USB Host shield. This wire can then be connected to the VIN on the Teensy 3.0. The USB Host shield will then get powered directly from the same USB port as the Teensy 3.0 and the VBUS will be 5V as required by most devices – note that you might need a separate 5V regulator depending on which device you are using with the shield, as it might draw too much current.
More information about how to modify the shield can be found at the hardware manual.
Also take a look at the guide for the other Teensy boards, as the wiring is almost the identical.
Hopefully this is just the first of many ARM based boards that is going to be supported by the USB Host shield library.
If you got any questions or comments, then feel free to write a comment below and I will answer as fast as possible.
Update
Both the Teensy 3.1 and Arduino Due is now also supported by the library.
Written by Oleg Mazurov  E strobe train
Traditionally, Toshiba HD44780-compatible alphanumeric LCD displays are driven by bit-banging bus signals combined with long delays between sending commands and data. In many cases this method is good enough. There are other cases as well where extra CPU cycles are not available and more economical method of driving a display is needed. I’m currently working on a design involving very fast USB exchanges combined with occasional LCD output and developed a solution which works very well for me. I’m posting it with hope that my fellow developers will find it useful.
HD44780 displays have been around for a long time. The internet provides plenty of posts about them, code samples and even a Wikipedia article. My favorite introductory text on the topic is Dincer Aydin’s LCD Info page.
PIC24 16-bit microcontrollers from Microchip have been around for some time as well. They are cheap and powerful and the Microchip C30 compiler (free version available) is quite good. They are not as popular as their 8-bit counterparts from Microchip and Atmel therefore good PIC24 resources are scarce. One nice introductory text on the topic can be found at Engscope.
Since I’m trying to minimize CPU time spent driving the LCD let’s first talk about timing in general. When developing for HD44780 we need to deal with 3 different times. First is the timing of the display part – the screen we see. LCD glass is very slow. When we attempt to update the screen faster than say twice a second the symbols become blurry and pale. The fastest display in my collection still looks OK when updated at 4Hz rate (250ms), while most others are twice as slow.
On the other hand, display data bus timing is many times faster. In order to write to the display we first need to set RS, RW and data lines, wait a little, then assert E line, wait some more and then de-assert it. If we are reading from the display we will also need to wait a little more after de-asserting E before we can read the data on the bus. Total bus cycle length is ~2.5us, which is 200 000 times less than the update rate of typical LCD glass. This time is pretty short but the MCU is still faster – a PIC24F clocked at 32MHz has an instruction cycle of 62.5ns and in 2.5us it will be able to execute 40 instructions. Therefore, no matter how simple it looks, it is preferable not to bit-bang the bus.
The third timing we need to deal with is command execution time. All but two LCD commands have stated execution time of 40us. Two slow commands – Clear and Home require 1.64ms to finish. Those are datasheet numbers, in reality the fast command on a modern display may finish in as low as 10us and slow commands on an old display can take as much as 3.5ms, depending on the age and the particular “HD44780-compatible” controller used. It is about 100 times faster than the glass.
Continue reading Driving a character LCD using PIC24 Enhanced Parallel Master Port
Written by Oleg Mazurov  Arduino reading digital scale
I am the proud owner of Stamps.com Model 510 5lb digital scale. It is a nice little scale which works very well (much better than Stamps.com service itself) while attached to my workstation. The scale doesn’t have a display making any kind of standalone use difficult. However, since the scale is a USB HID device reading data from it should be as easy as from a joystick and Arduino board should be adequate to provide a display function for it. To test this theory I made a simple setup consisting of Arduino UNO, USB Host shield and HD44780-compatible LCD display. I also wrote a small sketch which polls the scale and outputs the weight. The secondary objective of this project was to demonstrate LCD support in USB Host shield library.
For this project I used the following:
- An Arduino board. Standard size board, such as UNO, Duemilanove or Leonardo, will work
- USB Host Shield
- Toshiba HD44780-compatible LCD display, in 16×1 or 16×2 configuration. If you’re planning to use this sketch for something else, like data logging, the display is optional – all output from the scale is repeated to the serial port
- Stamps.com 5lb digital scale. Scales are standard HID devices with usage table 0x8d, therefore, scales from other brands may work as well with no or minimal modifications to the code
- USB Host library
The example code is also hosted at github, as well as in ‘examples’ section of the library under ‘HID’. It has been tested with Arduino IDE version 1.0.5.
In this project, the LCD is connected to the shield’s GPOUT pins, as documented in max_LCD.h header file. In addition to data lines, 5V and ground must also be connected to the shield’s 5V and GND terminals; the RW pin must be grounded – I do it on the LCD itself. In order to see the characters, the display must be biased – a 5K-10K pot with wiper on Vo and other two pins on 5V and ground will provide contrast adjustment.
Continue reading Adding a display to a digital scale using Arduino and USB Host shield
Written by Oleg Mazurov  Power switch populated
About a month ago I started shipping USB host shields built on PCB bearing revision number 2.0.1. On this PCB I added a new feature, suggested by Andrew Kroll – a VBUS power switch. The board comes with power switch unpopulated and if you don’t care about this feature it can simply be ignored. However, if you do care about power control, read on.
The ability to turn VBUS on and off at will can be very beneficial. In battery-powered projects the run time can be significantly increased by powering on USB device only when needed. Some other devices can’t even be initialized reliably without a powercycle. Also, many power switches incorporate current limiting circuitry allowing VBUS overload detection and prevention.
An example of populated power switch is shown in the title picture (click on it to make it larger). A is a power switch IC (in this case, Micrel MIC2004). B is 0.1uF ceramic capacitor in 0603 package. C is a wire from MAX3421E GPX pin to the ENABLE pin of the power switch. Finally, D is VBUS Power jumper which needs to be opened, as pictured. Current revision of USB Host 2.0 library is needed to support power control.
 Board Layout
Next picture will be used to explain the details of the power control circuitry.
-
Arrow A points to the jumper which needs to be cut open
-
Arrow B shows the position where 0603 0.1uF ceramic capacitor needs to be placed
-
C and D show the places for the power switches (only one switch is needed). Many switches packaged in SOT23-5 and SOT23-6 use this footprint, use On Semiconductor NCP380 as a reference. Also, some other 5 pin switches, such as Maxim MAX4793 and Micrel MIC20xx, will work while placed on SOT23-6 footprint, as shown on the title picture.
-
Certain switches, such as 6 pin NCP380, allow for adjustable current limit. The position for current setting 0603 resistor is marked ILIM – for the value of this resistor consult the datasheet for the part you’re planning on using
-
Many switches provide FAULT pin to signal various fault conditions, like output overload, reverse votage, or over-temperature. The pin is typically active low open drain type. It is broken out to a pad labelled VBUS OVL. The signal can be used in several different ways. A LED with a series resistor can be connected across VBUS OVL and a power rail. Also, it can be connected to a MCU input. In this case, a position labelled 10K should be populated with 0603 resistor, typical value is 10K. The other (upper) end of the resistor is connected to 5V rail with a trace which is placed under the letter K; if 3.3V level signal is desired, cut the trace and solder the upper end of the resistor to the 3.3V rail.
-
The power control signal is labelled VBUS EN. The library uses GPX pin for
vbusPower() and Init() functions. There is also a variant of Init() function which will hold the VBUS off for the number of milliseconds passed to it as a parameter. See usbhost.h file for details. Also, testusbhostFAT.ino demonstrates usage of powercycling Init() .
Continue reading VBUS power control on USB Host shield
Written by Oleg Mazurov  Beagle Analyzer USB hub trace
I’m the proud owner of Totalphase Beagle USB 480 protocol analyzer. It helps tremendously in debugging USB code and the software which translates binary traces into human-readable form is free allowing sharing the trace files. Some time ago I needed to capture and share analyzer traces of certain Bluetooth dongles with developers of USB Host Shield 2.0 library. Instead of sharing the traces privately I decided instead to put them into another GitHub repo for everyone to see and learn.
At the moment, the repository contains just a handful of Bluetooth traces, captured on Windows and Linux machines. I will be expanding the repo with other interesting traces generated during my development. Also, if anyone wants a trace from a device not already in the repo – just ask.
Enjoy,
Oleg.
Written by Oleg Mazurov  Mass Storage
The code supporting USB Mass Storage Class of devices has been added to USB Host Shield 2.0 library and is available to download on GitHub. Mass storage devices include USB Flash drives, memory card readers, external hard drives/CD-ROMs, smartphones/tablets, and some others – almost anything that shows as a drive while connected to a PC (exceptions are digital cameras as well as some phones pretending to be digital cameras). Andrew Kroll (who made this release possible) – thank you very much!
At present, the code example, also featuring Andrew’s FAT and extended memory implementation, can only be run on “big” Arduinos such as Mega and Mega 2560. Another FAT implementation, developed by Alex Glushchenko, is being tested – there is a slight possibility that at least some functionality can be demonstrated on a regular UNO board. On the other hand, the mass storage component can be used without a file system by simply reading/writing physical sectors; this approach can save a lot of memory. The documentation for the mass storage class code is available here.
Many hours has been spent testing the code; it should work with any device which claims to support “mass storage bulk only” transport. While newer (less than 5 years old) won’t cause any problems, older ones could be finicky. If your device shows odd behaviour with this code, please let me know – I will trade it for the good working one.
Enjoy!
Oleg.
Written by Oleg Mazurov  CO2 Soldering
Reflow soldering in toaster oven or on a skillet is popular among hobbyists and small-scale manufacturers. The process is simple and the equipment necessary is inexpensive and readily available. The results are very good if several simple rules are followed. One of these rules is to use freshly made PCBs – the shelf life of hot air leveled tin PCB finish is 6 months. A PCB which was used close to the end or past its shelf life will exhibit poor solder wetting resulting in bad joints.
Poor wetting can be overcome by increasing soak time and/or rising reflow temperature to give solder flux more time to act on oxide layer formed on the PCB finish during storage and reflow. This approach worked well in good old times of leaded solder, however, modern lead free solder reflow temperature is already quite high and increasing it may not be possible. In this case, soldering in inert atmosphere could be better option. In this article I will explain the process that I have started using some time ago – with great success.
Conceptually, soldering in inert atmosphere is easy: substituting air (which contains oxygen) in the oven with inert gas eliminates the cause of oxidation. The best gas for this purpose is nitrogen; it is non-reactive at soldering temperatures and being the major component of air it is the cheapest of all industrial gases. Being air-like it is also easy to use – all that is needed is a constant low volume flow into the oven during soldering cycle.
Continue reading Reflow Soldering in Inert Atmosphere
Written by Oleg Mazurov  TM240A building USB Host Shields
Some time ago I noticed that I’m spending more time building boards and less time developing and needed to increase my manufacturing capabilities. After thorough reading Dangerous Prototypes’ Chinese desktop pick and place machine forum thread I got in contact with a factory and bought TM240A – the big brother of TM220A. Earlier this week a DHL van carrying 70kg crate pulled in my driveway. After a day of hands-on learning I started building boards. This article was written after 2 days of using the machine and contains my first impressions as well as a couple of hints.
First, it is a real Chinese machine – well built, simple, and reasonably priced. At the same time, an owner must be prepared to fix mechanical issues and work around software bugs without relying on manufacturer’s support – the folks at Neoden are helpful but due to a time difference a reply to an e-mail would arrive the next day. Fortunately, the user base for these machines is expanding and the thread linked above as well as videos by Ian@DP and other people provide lots of useful info.
I was ready to face issues like air lines clogged by small pieces of styrofoam, non-functioning vacuum pumps and such; luckily, the only problem out-of-the box was racked gantry causing feeding fault. Thanks to this post in DP thread I was already aware about the symptoms as well as the fix – so I fixed it. While doing this I learned that to implement the fix no tools were necessary – a typical human finger jammed between the front support and the gantry works just as well as originally specified screwdriver.
I loaded some tapes and proceeded to stuffing boards. During test runs double sided removable scotch tape placed over the pads helped keeping parts in place. “Removable” type is preferable since it leaves no residue. Also, since the machine has no vision, accurate board registration is paramount. Here is how I do it.
Continue reading Neoden TM240A Pick and Place machine – first impressions
|
|